Mn13Cr2 Ball Mill Liner
Short Description:
Product Description
High Manganese Steel Mn13Cr2 Ball Mill Liner in general refers to a kind of casting steel with the Manganese content at 11%~22%, the carbon content at 0.9%~1.5%, mostly higher than 1.0%. Under low impact load, Manganese Steel Ball Mill Liner can achieve HB300~400, Under high impact load, can achieve HB500~800. Different impact load, the High Manganese Steel Mn13Cr2 Ball Mill Liner's surface hardening layer depth can be up to 10~20 mm. High hardness of hardening layer can resist the wear of grinding media. Under the condition of strong impact abrasive wear, High Manganese Steel Mn13Cr2 Ball Mill Liner has excellent anti-wear performance, so High Manganese Steel Mn13Cr2 Ball Mill Liner widely used in mining, aggregates, coal industries as wear-resistant parts.
Note: Depending upon the various application, we propose suitable profile with appropriate alloy ranging from 12 to 25%.
Chemical Elements
Name |
Chemical Elements (%) |
|||||||
C |
Si |
Mn |
Cr |
Mo |
Ni |
P |
S |
|
High Manganese Steel Mn13Cr2 Ball Mill Liner |
0.9-1.5 |
0.3-1.0 |
11-22 |
0-2.5 |
0-0.5 |
≤0.05 |
≤0.05 |
≤0.05 |
Physical Property & Microstructure
Name |
HB |
Ak(J/cm2) |
Microstructure |
Manganese Steel Ball Mill Liner |
≤280 |
≥100 |
A+C |
A:Austenite C:Carbide |
Product Package
● Steel Pallet, Wooden Pallet and Wooden Box
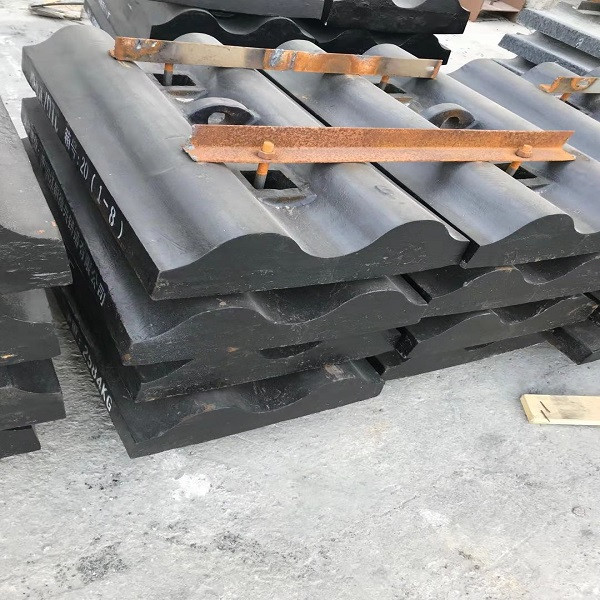
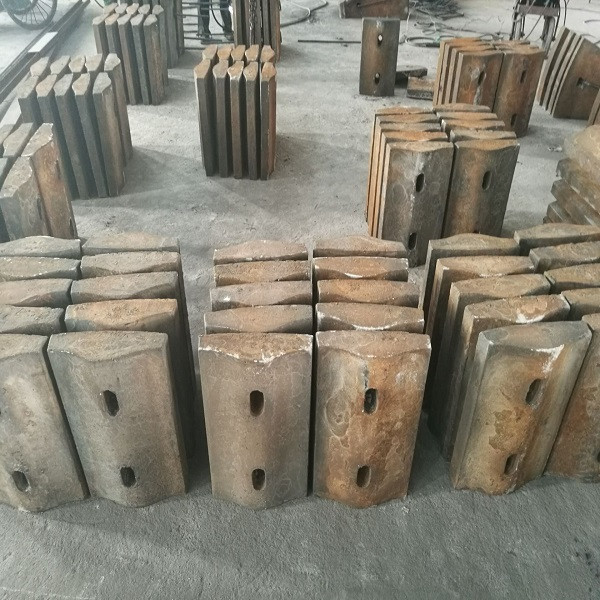
● Customized according to special packing requirement.
Application
Our High Manganese Steel Mn13Cr2 Ball Mill Liner are widely used in the grinding stage for mining industry, cement industry, thermal power plant, paper-making and chemical industry etc.
A ball mill is a type of grinder used to grind, blend and sometimes for mixing of materials for use in mineral dressing processes, paints, pyrotechnics, ceramics and selective laser sintering. It works on the principle of impact and attrition: size reduction is done by impact as the balls drop from near the top of the shell.
A ball mill consists of a hollow cylindrical shell rotating about its axis. The axis of the shell may be either horizontal or at a small angle to the horizontal. It is partially filled with balls. The grinding media are the balls, which may be made of steel (chrome steel), stainless steel, ceramic or rubber. The inner surface of the cylindrical shell is usually lined with an abrasion-resistant material such as manganese steel or rubber lining. Less wear takes place in rubber lined mills. The length of the mill is approximately equal to its diameter.
When it comes to austenitc manganese steel mill liners, H&G Mill Liners had focused this material for long time. Our austenitc manganese steel mill liners span life more than other foundries mill liners.
This material used for grid liners, and generally smaller mills. Its great advantage is that it work hardens under stress, yet the substrate remains tough and can withstand extreme impacting without fracture. Its primary disadvantage is that it spreads with impact, so solid liners begin to squeeze together and become extremely difficult to remove, and can damage a mill shell if the stress is allowed to build up to an extreme level.
Austenitic manganese steel’s ability to work harden from impact loading along with its exceptional toughness make it the best wear material choice for many demanding applications.The hardness of manganese steel in the solution annealed and water quenched condition is normally around 220 HB. It is possible to strain harden this material to approximately 500 HB. In order to achieve this high hardness level, the impact loading must be high while the material wearing away from gouging abrasion is limited. It is typical in crushing applications were the main wear mechanism is gouging abrasion that the manganese steel will harden to some intermediate level, typically 350-450 HB.
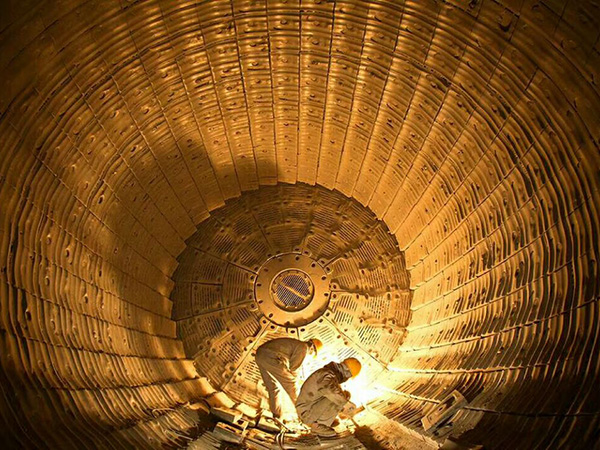
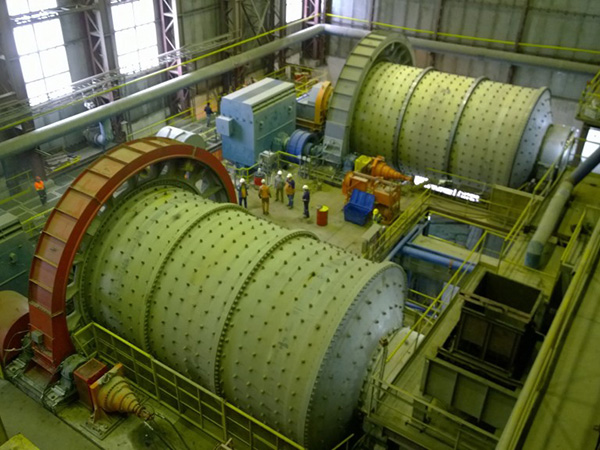
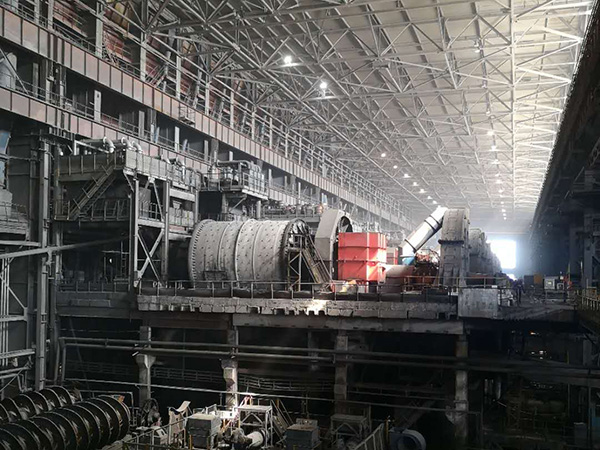