High Chrome Mill Liner for Metso Mining Machines
Short Description:
Product Description
White Iron Ball Mill Liner in general refers to the alloy white iron with the chromium content at 12%~26%, the carbon content at 2.0%~3.6%. White Iron Ball Mill Liner distinctive features is that the M7C3 type eutectic carbide micro hardness is HV1300~1800. White Iron Ball Mill Liner’s eutectic carbide is distributed on the base, martensite(the most hard metal matrix organization), in discontinuous network and isolation, which reduces the fragmentation of the matrix effect. As a result, the high chromium Ball Mill Liner has high strength, strong toughness and good wear resistance features , which is widely used at Mining ,Cement and power industry.
White Iron Ball Mill Liner is recommended to be using at low impact working condition such as:
1. Belt conveyor liner for Mining industry.
2. Cement plant Ball Mill.
3. Chemical industry Ball Mill.
Chemical Elements
Name |
Chemical Elements (%) |
|||||||
C |
Si |
Mn |
Cr |
Mo |
Cu |
P |
S |
|
High Cr Ball Mill Liner Cr26 |
2.5-3.3 |
0-0.8 |
≤2.0 |
23--28 |
≤3.0 |
≤1.2 |
≤0.06 |
≤0.06 |
High Cr Ball Mill Liner Cr15 |
2.3-3.3 |
0-0.8 |
≤2.0 |
14--18 |
≤3.0 |
≤1.2 |
≤0.06 |
≤0.06 |
Physical Property & Microstructure
Name |
HRC |
Ak(J/cm2) |
Microstructure |
High Cr Ball Mill Liner Cr26 |
≥58 |
≥3.5 |
M+C+A |
High Ball Mill Liner Cr15 |
≥52 |
≥4.5 |
M+C+A |
M-Martensite C- Carbide A-Austenite |
Note: Adjust the chemical content or add other alloying elements of Ball Mill Liner according to customer needs is available.
Product Package
● Steel Pallet, Wooden Pallet and Wooden Box
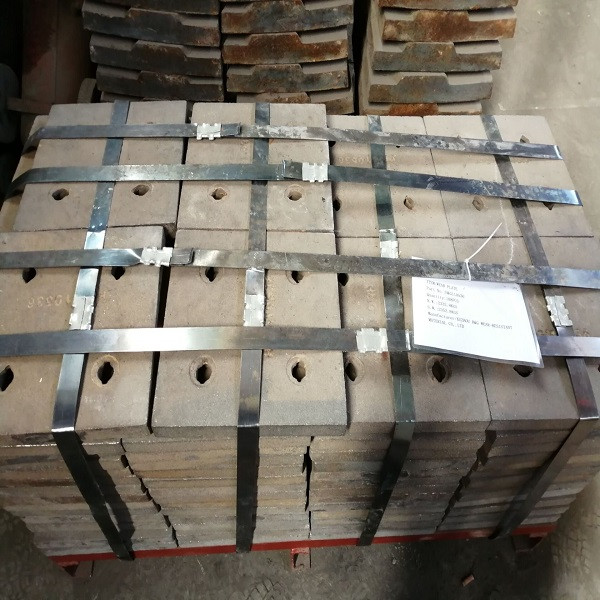
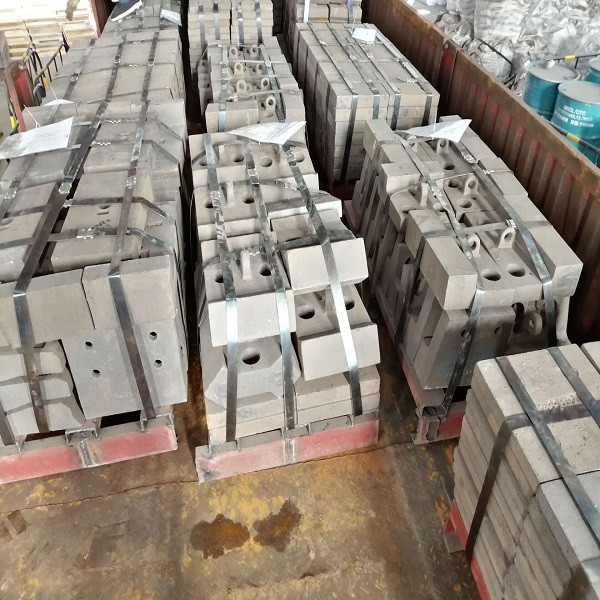
● Customized according to special packing requirement.
Application
Our White Iron Ball Mill Liner are widely used in the grinding stage for mining industry, cement industry, thermal power plant, paper-making and chemical industry etc.
A ball mill is a type of grinder used to grind, blend and sometimes for mixing of materials for use in mineral dressing processes, paints, pyrotechnics, ceramics and selective laser sintering. It works on the principle of impact and attrition: size reduction is done by impact as the balls drop from near the top of the shell.
A ball mill consists of a hollow cylindrical shell rotating about its axis. The axis of the shell may be either horizontal or at a small angle to the horizontal. It is partially filled with balls. The grinding media are the balls, which may be made of steel (chrome steel), stainless steel, ceramic or rubber. The inner surface of the cylindrical shell is usually lined with an abrasion-resistant material such as manganese steel or rubber lining. Less wear takes place in rubber lined mills. The length of the mill is approximately equal to its diameter.
When it comes to chrome moly white iron mill liners, H&G Mill Liners had focused this material for long time. Our chrome moly white iron mill liners span life more than other foundries mill liners.
This cast material is considered to be the ultimate developed and used to date for abrasion resistance in Milling. It is commonly used in cement mills and some of the largest Ball Mills in the world and where performance has not been bettered to date.
The Features
- 600 to 700 BHN white iron
- Large ball mills
- Malleable Iron: cast as white iron,then malleabilised, or heat treated, to impart ductility. Consists of tempered graphite in an a-ferrite or pearlite
matrix - Common in cement mills
- Used for abrasion resistance
Ball Mill Liner Installation
- Before installing the ball mill liners, you should know how many pcs old mill liners need to exchange.
- Ask an expert to arrange and coordinate the entire replacement process. All exchange need based on work drawings.
- It is necessary to circulate the remaining pulp in the ball mill as much as possible, remove the rubber pad of the waste liner, clean the protruding point of the wall of the ball mill, and remove dust and descale the cylinder. When cleaning the work, it is necessary to fix the barrel of the ball mill. The workshop needs to have good ventilation conditions and suitable temperature. Then the installer can enter the ball mill barrel to start the operation.
- When removing the old ball mill liner, first remove the used lining screws, then remove the old ball mill liner one line after one line, and then lift the used ball mill liner. When removing the liner, the person should pay attention to safety and pay attention to the standing position to avoid being injured by the ball mill liner.
- The new liner of the ball mill should be installed to ensure that the gap during the period is within the required range. Fix the spiral of the ball mill liner. Carefully seal the packing and gasket to prevent leakage of mineral powder. If there is no gasket, it should be wrapped around the corresponding position. Two rounds of cotton cord or hemp plus lead oil. At the same time, it is necessary to apply a layer of cement mortar on the inner wall of the cylinder and screw it tightly before solidification. It should be noted that the thin end of the step liner should be consistent with the direction of the arrow in the direction of rotation of the mill.
- After the replacement, the ball mill staff needs to confirm that there is no person, no working tools, and other needless things in the cylinder, and it is necessary to carefully check the inside and outside of the cylinder before closing the empty cover.
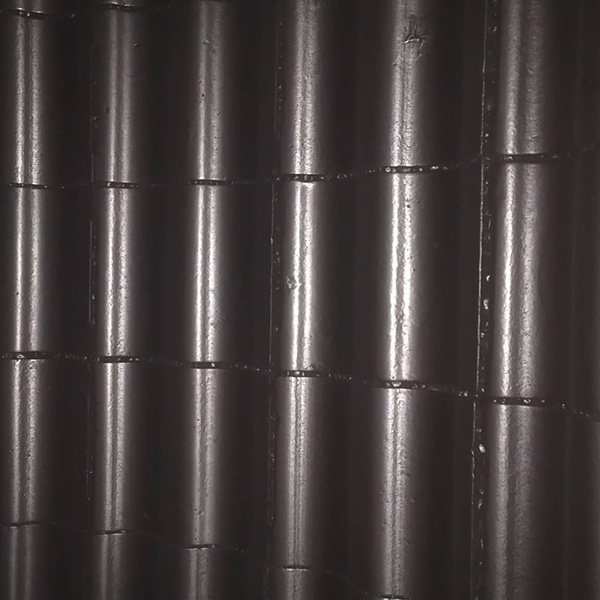
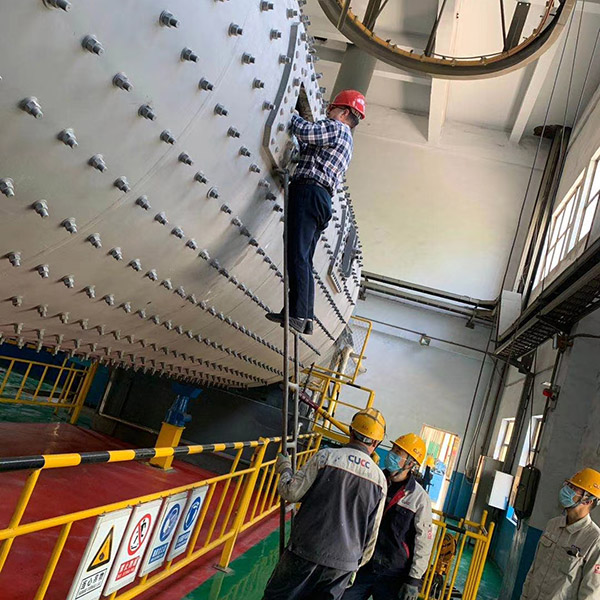
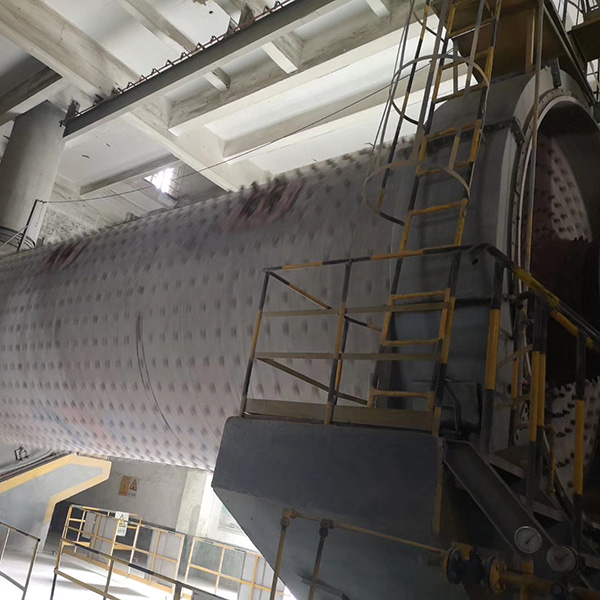
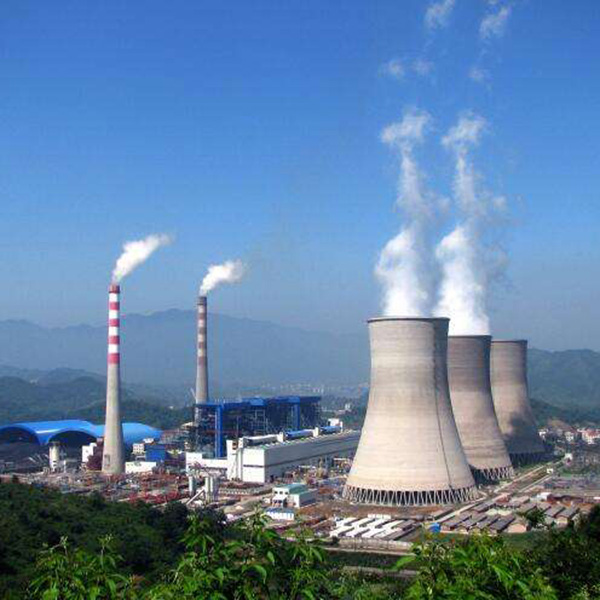