Citic SAG and AG Mill Liner
Short Description:
Product Description
SAG Semi-Autogenous Grinding Mill Liner and AG Autogenous Grinding Mill Liner from H&G use Cr-Mo materials (AS2074 Standard), SAG Semi-Autogenous Grinding Mill Liner and AG Autogenous Grinding Mill Liner provides superior impact and wear resistance in all semi-autogenous milling applications.
To choose the right material for the right application is our mission , we are always working together with our customer to achieve this .The right material is upon to:
1. The mineral ground
2. Milling data information
3. Maximum grinding media diameter (mm)
4. Grinding media filling degree (%)
In general, Item M1 used for high impact condition ,P1 used for low impact condition. It shall change according to your mineral processing.
Specification Available
Code |
Chemical Elements(%)SAG Semi-Autogenous Grinding Mill Liner and AG Autogenous Grinding Mill Liner |
|||||||
C |
Si |
Mn |
Cr |
Mo |
Cu |
P |
S |
|
P1 |
0.6-0.9 |
0.4-0.7 |
0.6-1.0 |
1.8-2.5 |
0.25-0.5 |
0-0.5 |
≤0.04 |
≤0.06 |
M1 |
0.3-0.45 |
0.4-0.7 |
1.3-1.6 |
2.5-3.5 |
0.6-0.8 |
0-0.5 |
≤0.04 |
≤0.06 |
Physical Property & Microstructure
Code |
Hardness(HB) |
Ak(J/cm2) |
Microstructure |
P1 |
325-375 |
≥50 |
P |
M1 |
350-400 |
≥75 |
M |
M-Martensite, C-Carbide, A-Austenite, P-Pearlite |
Note: Adjust the chemical content or add other alloying elements of SAG Semi-Autogenous Grinding Mill Liner and AG Autogenous Grinding Mill Liner according to customer needs is available.
Product Package
● Steel Pallet, Wooden Pallet and Wooden Box
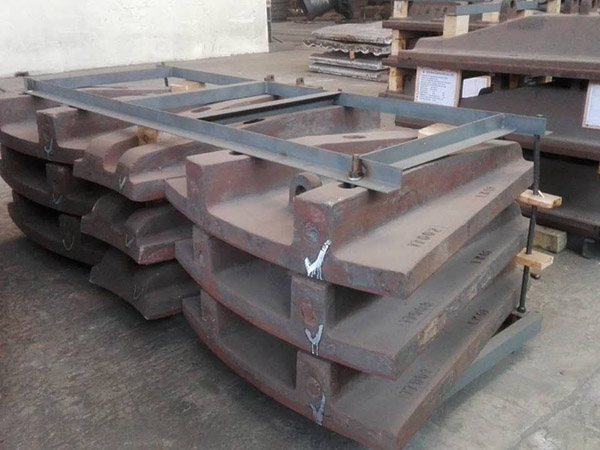
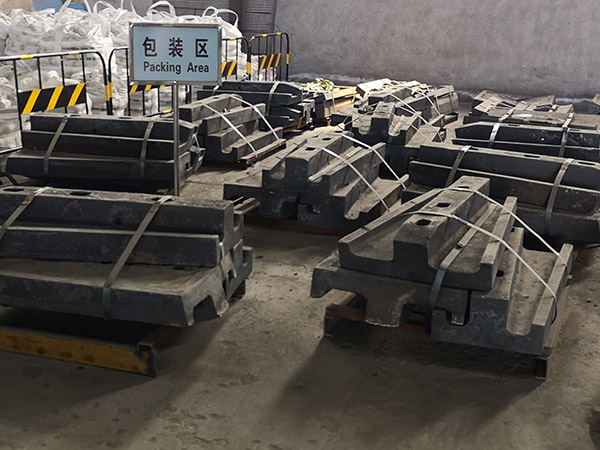
● Customized according to special packing requirement.
Our Advantage
At HG Casting, we engineer innovative designs, tailored especially for every customer. Our SAG Semi-Autogenous Grinding Mill Liner and AG Autogenous Grinding Mill Liner are manufactured to the highest industry standard for Autogenous Grinding(AG), Semi-Autogenous Grinding(SAG), Primary / Secondary and re-grind rod or ball mills. MGS Casting mill lining system designed by our highly trained, and dedicated team throughout the world has taken your entire comminution circuit into consideration. Supporting our front line Mill Engineers is a large team of extremely specialized design engineers, material chemists, manufacturing and logistics experts responsible for delivering exceptional service.
Optimal mill designs engineered by our team take into consideration service life; grind & power efficiency and ore characteristics, along with costumer circuit constraints both up and downstream of the mill lining.
HG Casting had success to use ASTM 2074/L2B alloy steel to manufacture AG/SAG mill liners. Under this material, our mill liners span life can be obviously improved. Our Australia customers had ordered more than 10,000 tons per year of this material mill liners.
As a casting foundry, HG Casting also has own SAG Semi-Autogenous Grinding Mill Liner and AG Autogenous Grinding Mill Liner design. In general terms, lifter spacing and angle, grate open area and aperture size, and pulp lifter design and capacity must be considered. Each of these topics has had a considerable amount of research, and numerous case studies of evolutionary liner design have been published. Based on experience, mill liner designs have moved toward more open shell lifter volumetric capacity and a grate design to facilitate maximizing both pebble-crushing circuit utilization and SAG mill capacity. Mill throughput is maximized with shell lifters between ratios of 2.5:1 and 5.0:1. This ratio range is stated without reference to face angle; At equivalent spacing-to-height ratios, lifters with greater face angle relief will have less packing problems when new but experience higher wear rates than those with a steeper face angle. Pulp lifter design can be a significant consideration for SAG mills, particularly for large mill. All mill sizes increases, the required volumetric capacity of the pulp lifters grows proportionally to mill volume.
Semi-autogenous grinding mill liner also called SAG mill liner, Autogenous grinding mill liner also called AG mill liner. Since the 2014 year, H&G Machinery has had become one of the largest AG/SAG mill liner manufacturers from China. No matter which material you want, manganese steel or Ni-hard steel or Cr-Mo steel or alloy steel; No matter which type of your mill liners need. wave shape or raised edge shape or stepped shape; H&G Machinery is your first choice.
Which Choose H&G Machinery’s AG/SAG Mill Liners?
- Rich experience. H&G Machinery supplies more than 10,000 tons of various kinds of mill liners.
- Various material. We offer different materials to suit different work conditions. Such as manganese steel, Ni-hard steel, Cr-Mo steel, and other alloy steels.
- Complete QC system. H&G Machinery supply a complete quality control system and records. You can check all the documents and records when you visit us or we send them to you.
- OEM service. H&G Machinery can manufacture your liners by your design or our engineer design.
AG SAG Mill Liner Function
Semi-autogenous grinding and autogenous grinding is a powder mill with a large cylinder diameter and a slow rotation. The material is fed into the mill through the hollow journal at the feeding end. Under the interaction of the materials, the material crushed to a certain fineness passes through the discharge The hollow journal at the end is discharged out of the machine. The liner is an important part of the grinding machine.
- The lifting liner lifts the material to a certain height, the impact of the free fall, and the friction effect between the friction between the materials, so that the materials are crushed and finely ground.
- The shape of the end cover lining board is relatively special. The bulk materials are added through the feeding port. The small pieces of material fall uniformly on the bottom center of the cylinder along the surface of the wave lining and then diffuse to both sides, while the large pieces of material have greater kinetic energy. : The projectile point always tends to the far side, but part of it will inevitably collide with the two sides of the wave lining. Due to the counterattack effect of the wave lining, it can prevent the material from being “segregated” in the axial large and small pieces, so that the large pieces of material can be evenly distributed. The coarse material returned from the discharge end along the lower side, like the newly added material block, evenly falls on the center of the bottom of the cylinder and then diffuses to both sides. The large and fine-grained materials move in the opposite direction along the axial direction at the bottom of the simplified Chinese, so they have a grinding effect.
- Both the lifting T-shaped lining plate and the wave plate have the function of wedging the block. With the rotation of the mill, the position of the block increases, and the compressive force quickly disappears and becomes a tension when the “arched” bridge moves upward and collapses so that the instantaneous stress generated by the continuous reciprocating motion will cause the block The monomers are separated, resulting in grinding.
AG/SAG Mill Liners Installation
Preparation Work
- Prepare all need to replace mill liners.
- Check the shape and size of all liner plates, remove hair wings, casting slag, etc.;
- Be prepared to replace the required bolts, nuts and washers and other accessories;
- Check carefully whether lifting appliances, appliances and rigging are safe and reliable.
- Prepare 36V safety power supply for construction lighting in the tube;
- Before the mill is stopped, there must be enough minerals in the barrel suitable for the entry and exit of the liner before stopping.
- All construction personnel must wear labor protection supplies including hard hats, masks, and non-slip shoes before entering the site.
Installation Steps
- Remove the feed trolley and lift the receiving hopper;
- Remove the fixing bolts of the liner piece by piece to protect and clean up all screw holes. Do not dismantle more than 3 sets of liners at one time;
- Lift out the removed AG mill liners one by one by using the driving, and then hang the lining board to be replaced into the tube;
- Under the direction of the hoisting commander, use the vehicle to wear the wire rope through the bolt holes of the cylinder, pull the lining board to the required installation position, and then use the crowbar to straighten the screw and nut. Fill the two screw holes of the lining board alternately with hemp rings (not less than 5 in each group), install the leak stop rubber ring and flat washer and tighten the nut;
- When installing the mill liner, the deposits and debris at the installation location should be cleaned up;
- If it is found that the discharge trough of the grid plate installation site is seriously worn, the discharge trough must be replaced before the grid plate is replaced;
- Install the recovery feed trolley and mine funnel.
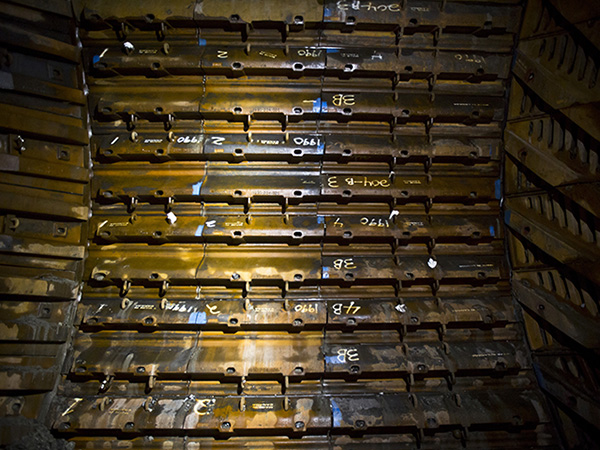
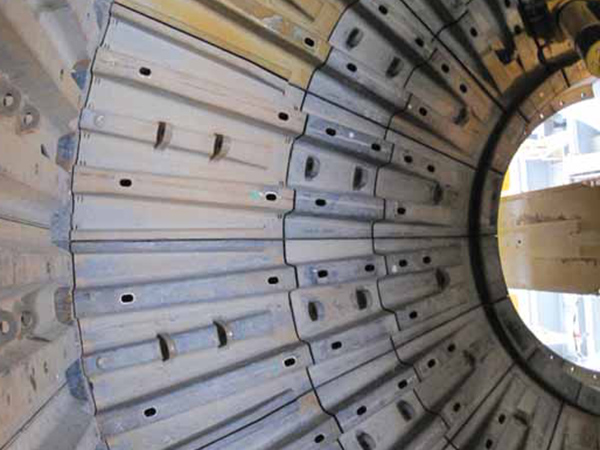
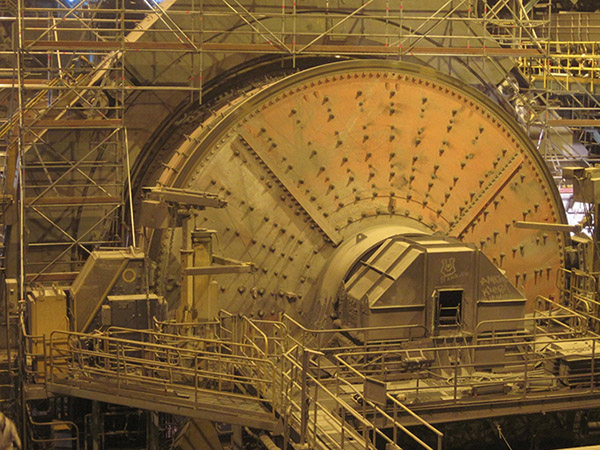
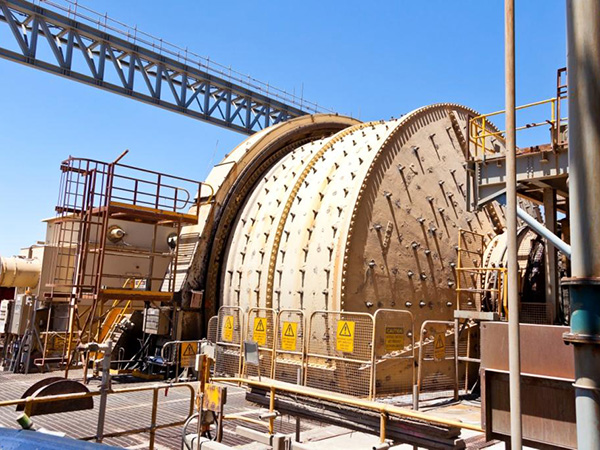