SBM Bowl and Mantle Liner
Short Description:
Product Description
CONE CRUSHER BOWL AND MANTLE LINER is manufactured with high manganese steel Mn13Cr2, Mn18Cr2, Mn22Cr2 or Manganese steel with special alloy and heat-treatment process. CONE CRUSHER BOWL AND MANTLE LINER has a working life of 10%-15% longer than those made of traditional manganese steel. As per the feedback from customers, the good performance of our CONE CRUSHER BOWL AND MANTLE LINER in different working condition greatly decreased the time of examination & repair and the use-cost.
MAIN BRANDS SUPPORT:
Metso, Sandvik, Barmac, SVEDALA, Omnicone, EXTEC, Maxtrak, Keestrack, Symons, Hazemag, Cedarapids, Telsmith, McCloskey, Trio, Powerscreen, Kleemann, Terex, Pegson, Kue Ken, Parker, Shanbao, SBM, Zenith, LIMING, MINYU and other famous brands.
Product Package
● Steel Pallet.
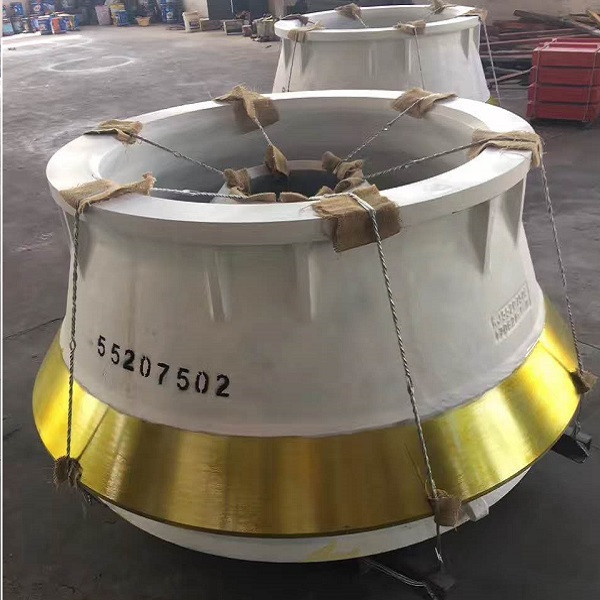
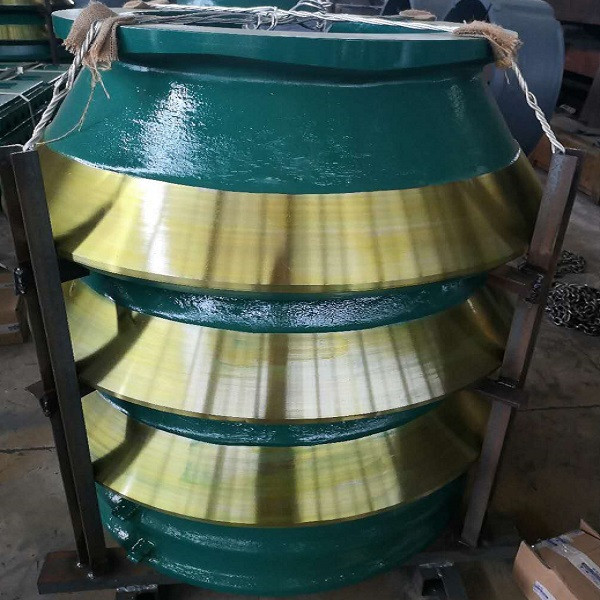
● Customized according to special packing requirement.
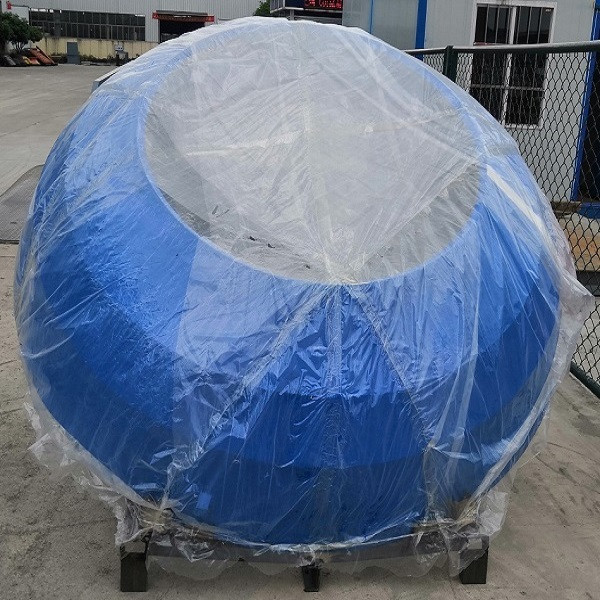
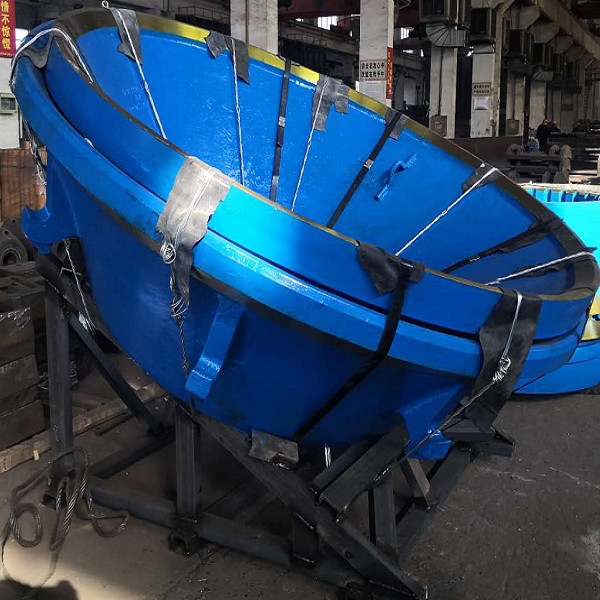
Application
Cone crushers are a type of compression crusher used by aggregate, coal, concrete, crushing, fracking sand, and mining industries, which reduces material by squeezing or compressing it until it breaks. Specifically, the material is compressed between an eccentrically rotating piece of steel, the mantle, and a stationary piece of steel, the bowl. The material works its way down along the crushing chamber as it gets smaller, until the crushed material discharges at the bottom of the machine. The final product’s sizing is determined by the gap setting between the two crushing members at the bottom also known as closed side setting.
Cone crushers are available in either a bushing, bearing and even a combination of roller bearing and sleeve bearings. The bearing cones run cooler and more efficient, allowing more applied horsepower to crushing rock than creating excess heat. The bushing cones require more lubricating oil and larger, more active oil coolers, but are less expensive to build and repair. The most often replaced parts in a cone crusher are the wear liners in the crushing chamber, which consist of the mantle and the bowl. When dealing with finer products, settings can be adjusted by adding a specialized liners, mantle, and concave ring that reduce the receiving opening and angularity between head and concave, allowing for a more specialized finished product.
Capacities and product gradations produced by cone crushers are affected by the method of feeding, characteristics of the material fed, speed of the machine, power applied, and other factors. Material hardness, compressive strength, mineral content, grain structure, plasticity, size and shape of the feed particles, moisture content will affect production capacities and gradations. Gradations and capacities are most often based on a typical, well-graded choke feed to the crusher. A choke feed is when the crusher cavity is kept full, without spilling out over the top of the crusher. A minimal feed is when the crusher cavity is kept fairly low, just enough to ensure the crusher continues to work. An anti-spin device can help with minimal or intermittent feeds.
Cone crushers are offered in a variety of configurations in order to meet any Producer’s crushing needs: liner configurations for larger or finer-sized material; minimal to choke feed for different crusher cavity volumes; stationary, track, and mobile (wheeled) crushers; and they can be used in the primary, secondary, tertiary, or quaternary position in the crushing circuit.
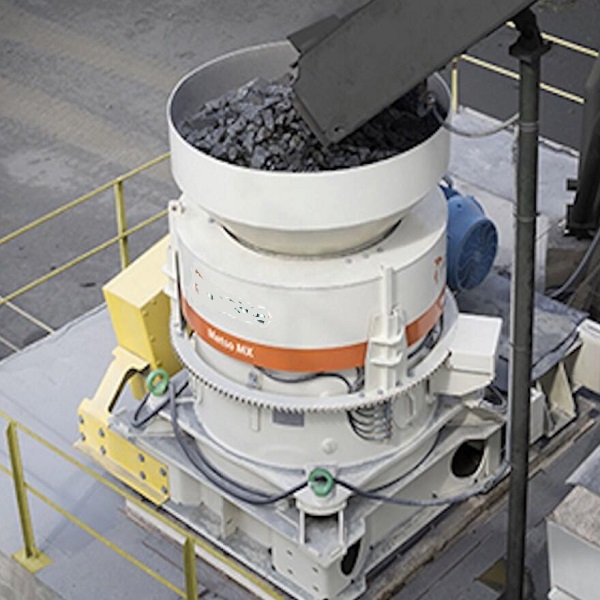
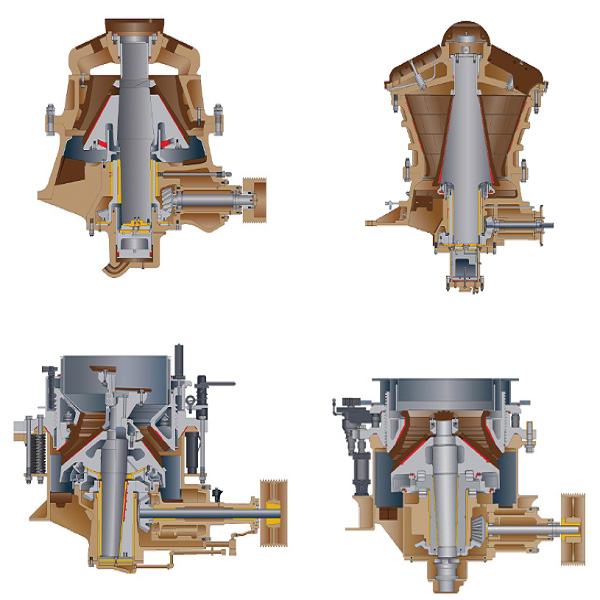